先週神奈川の天気は大幅に冷え込んだ、いつも夜9時前後でランニングしているが、今は手足が寒かった、いよいよ冬本番まで秒読みの感じだった。私自身は冬派で、寒くても別にちょうど気持ちよかった形で、ランニング距離が延びていた。
町に走っている電気自動車にとっては、これからは苦手のシーズンだよね。大体どちらの電気自動車でも、どんなに熱くなるまで走っていたとしても、24時間ほど放置すれば、大気温度とほぼほぼ同じところまで冷え込みする。氷点下の天気で、電池の冷え込みを防ぐために、わざと普段より少し長めに車を走行させて、あらかじめ暖機しておくやり方は実はあまり効果がない。少し反常識であるが、下記グラフを見れば、わかる。初期温度が高いほうは、大気温度との温度差もつくため、温度降下のスピードも速いのだ。
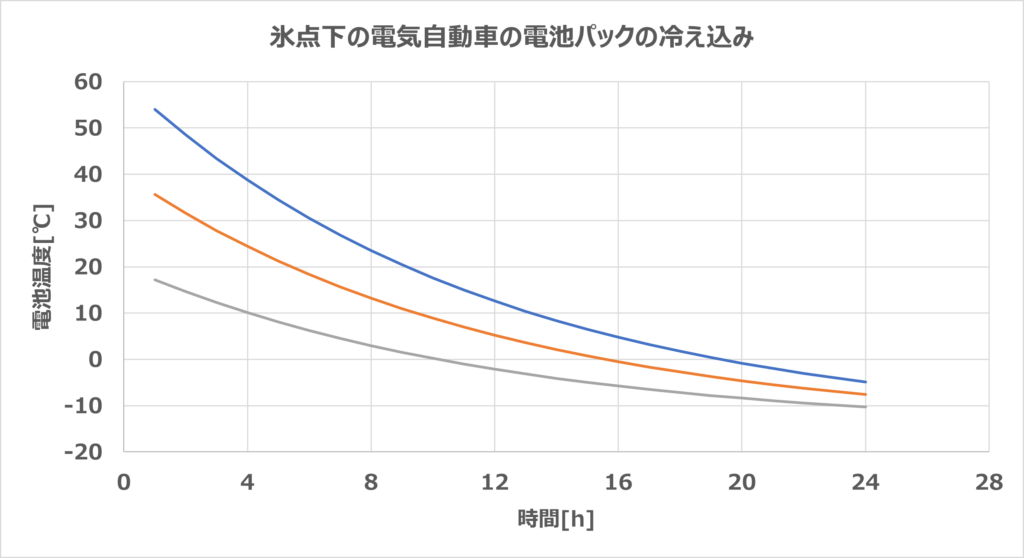
電池が冷えたら、いろいろ不便をもたらす。起動時の出力不足、充電スピード低下、電費悪化。。。車ユーザーさんにとって、どれでも悩ましいね。せっかく年末年始の長い休暇で、家族と一緒に東京から長崎のスキー場に旅を楽しんでいたのに、高速道路で車速低下してイライラ、電費消耗が早くて途中で電池ぎれを心配、しかも途中での急速充電で全く電力が補充できなくなり、想定以上の時間が高速道路で費やしてしまうことは誰でも経験したくない。
やっぱり、EVは、 キャビン空調とパワートレイン温調の両立は大事。ただし、従来のHVACと冷熱システムを用いてはそれが容易に実現できない。
下図のように、従来のHVACシステムと冷熱システムはチラーというユニットによってカップリングさせている。チラーとは、 片方に冷たい冷媒を流して、片方に熱いクーラントを流して、冷媒とクーラントの温度差を利用して、クーラントの熱を冷媒に移動させる装置である。チラーにおける熱交換で、コンプレッサーの冷却能力を一部冷熱回路に分流させて、冷熱回路で冷水が作られて、あっちっちになっている電池などを冷やせている。
このようなシステムの弱点と問題点は明白だ。
- 熱はOne-Way的に水回路からHVACにしか移動できない
- 乗客室内暖房とパワー系暖機は完全にヒーターに頼り、寒地では一気に大口で電力を食う
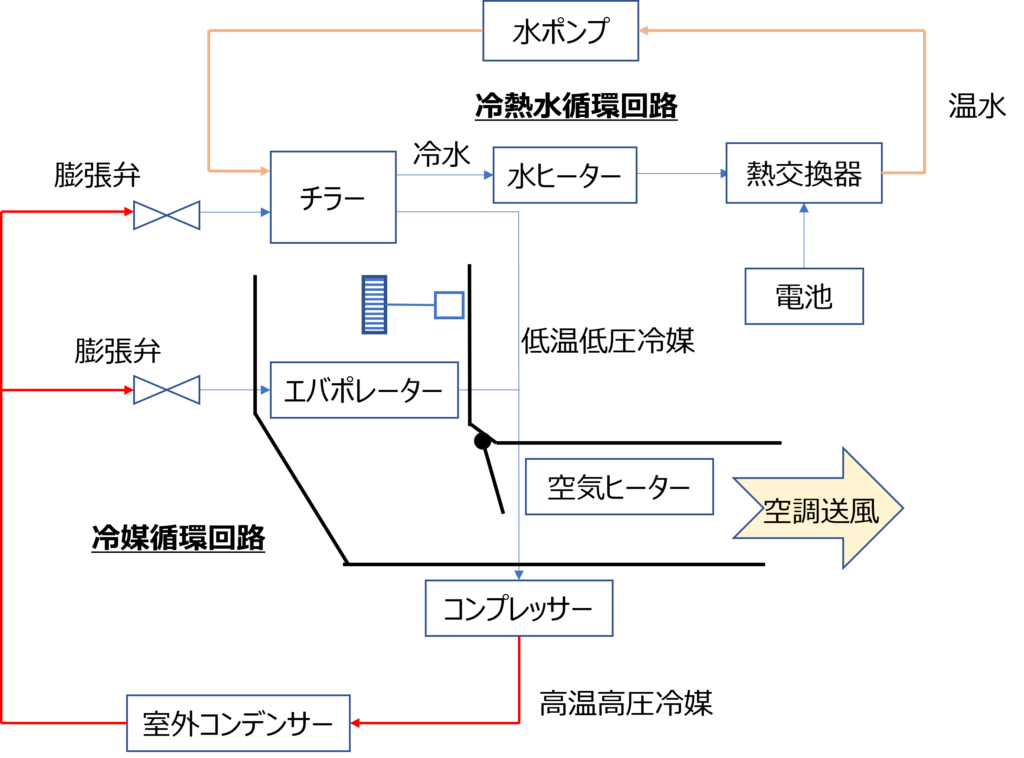
本章では、 キャビン空調とパワートレイン温調の 両立を図るために、空調/温調システムをEVに適したRedesignが必要だと考えており、考案した新しいシステム構想コンセプトとコンポネントを紹介したい。
まず、目の前の冬を考えると、電池を温める必要がある。従来のシステムは水ヒーターでクーラントを加熱している。では、このヒーターでどのぐらいのパワーを食っているかを簡単に計算したい。
電池の熱容量と電気容量は大体5:1の関係を持っている。60kWhの電池パックであれば、300kJ/Kの熱容量と大外れなく推定できる。
気温-3℃の朝で、出発する前に電池をあらかじめ22℃まで温めるとすると、必要なエネルギーは7500kJになります。電力に換算すれば、2.08kWhになります。熱損失3分の1で考えると、3kWh前後の電力は電池暖機に使わないといけない、これだけで20kmぐらいの走行距離は消えてしまう。さらに、30min間で急速に暖機して欲しければ、6kW程度の大型ヒーターを載せる必要がある。
エネルギーとしてもコストとしても、電池に専用なヒーターを付けることはもったいないし、ECOではないと考えておる。弊社の考案は下図の通りに、電池暖機専用のヒーターを取り外して、HVAC回路から熱を電池に効率よく運ぶ案を考えておる。
水冷凝縮器
水冷凝縮器とは、コンプレッサーから出てきた高温高圧の冷媒ガスを片方流して、片方はクーラントを流して、冷媒ガスとクーラントの温度差で、冷媒ガスの熱量をクーラント側に移動させる装置である。
改造した後に、冷媒とクーラントの間の熱移動はTwo-Wayになり、電気ヒーターの代わりに、冷媒から熱をもらって電池などの暖機に使える。
大口で電力を食う電気ヒーターに比べて、水冷凝縮器は全く電力が食わないから、熱交換に必要なパワーはコンプレッサーにて集約し、トータル的には電費の改善につながる。
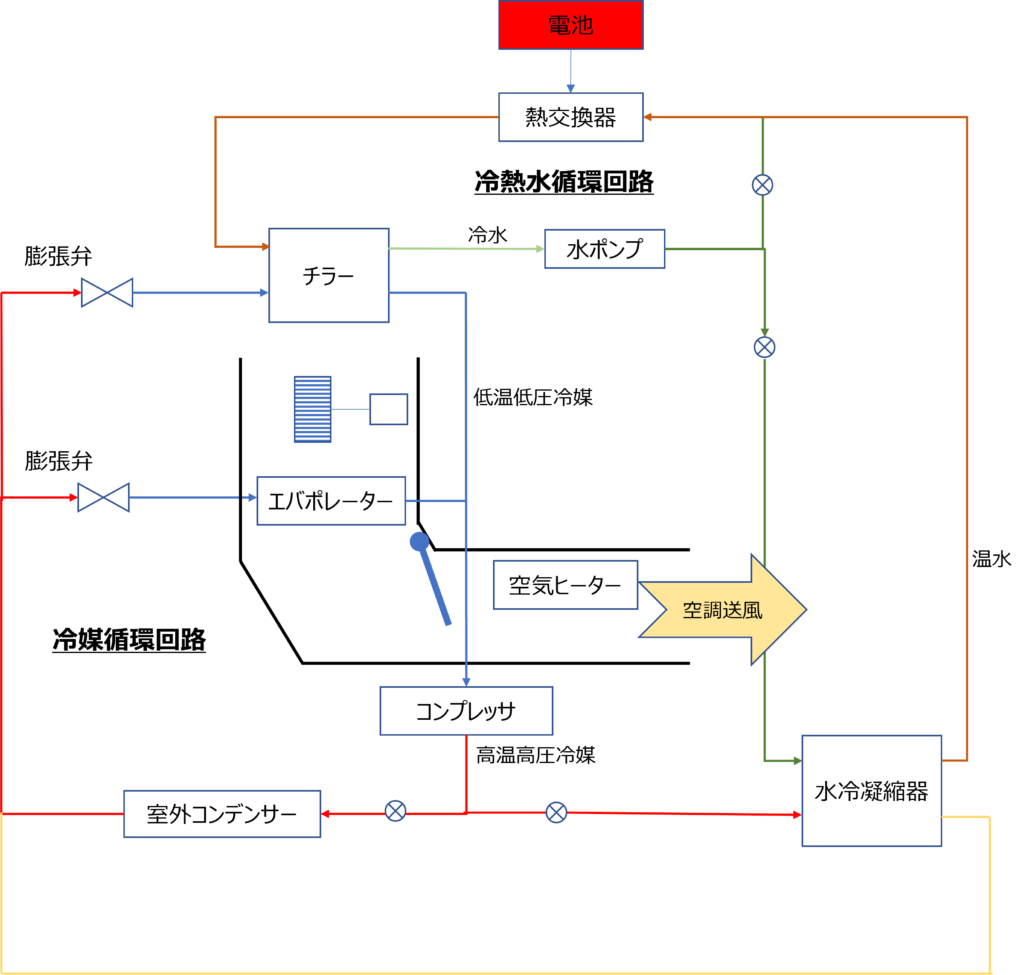
室内コンデンサー
さらに、室内コンデンサーを取り入れることで、電力を食う室内暖房用の空気ヒーターも取り外すことが可能。室内コンデンサーとは、高温高圧の冷媒ガスの熱をHVACダクトに通っている空気に移動させる装置である。コンプレッサーの仕事力で直接に空気を温めることができるようになる。これはいわばヒートポンプ式のカーエアコン方式であること。低温外気から熱を引いて、室内空気を温める素晴らしいアイデアだった。
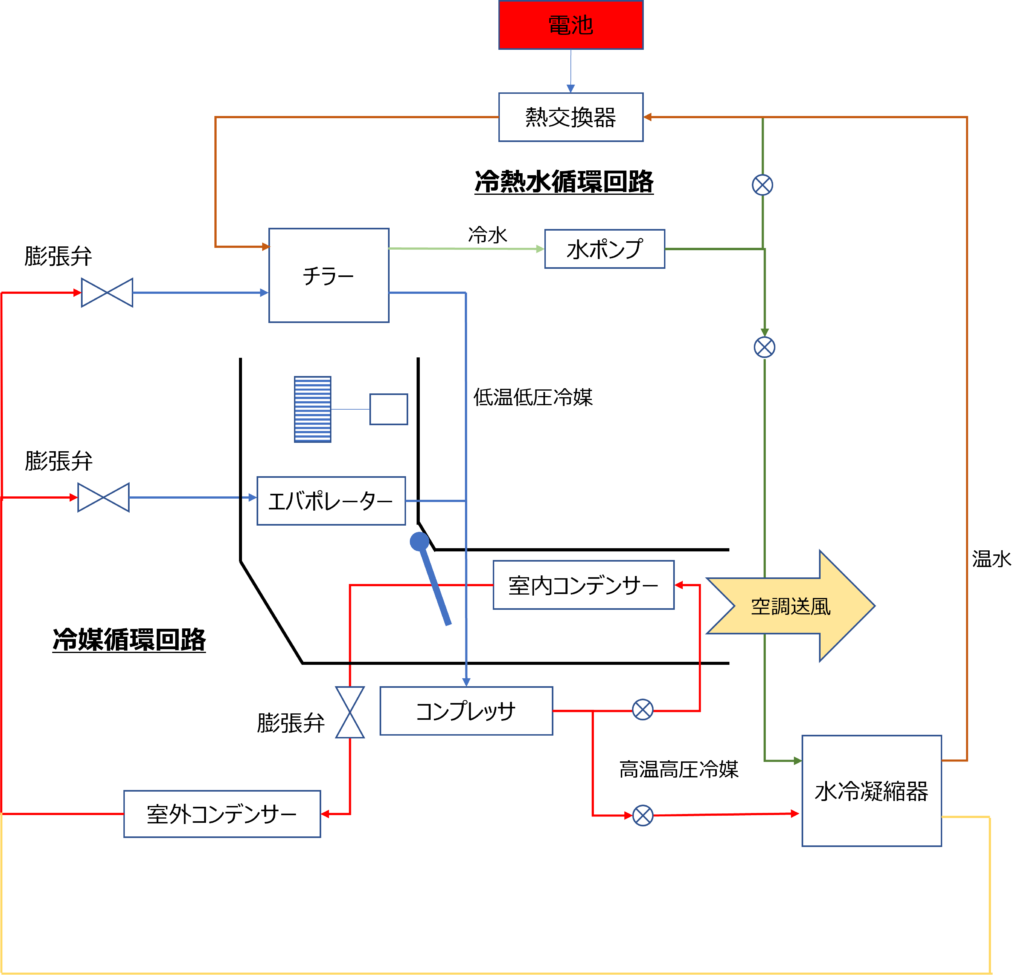
MBD開発
上記のようにRedesignされたシステムでは、冷力元と熱力元とも1箇所のコンプレッサーに集約されており、各作動モードに応じて、コンプレッサーの仕事力を調整し、各要求元に冷力と熱力を適切に分配しないといけない。しかも、コンプレッサーの仕事力はいろんな制約条件を受けている、例えば、騒音、車室内振動、電費、摩耗耐久性などとトレードオフする必要だ。簡単にいわば、従来のシステム設計よりは、ハードルがだいぶ高くなる。
開発組織にも大きい課題がある。システムは魅力的にもかかわらず、空調設計屋にはいきなり大きい負担を押し寄せることになってしまう。空調設計部隊のみで、システム全体を俯瞰して完全なシステム開発をリードするのは無理だと考察しておる。特に、縦割りの強い開発組織では、必要な情報すら収集することがかなりの体力をかかってしまう。電池の発熱量、必要加熱量はどうなっているか、冷却器の熱伝達係数はどうなっているか、水回路の損失はどうなっているか、いつ冷却するか、いつ加熱するか、いつNVHを何dB以下に収まらないといけないかなどなど膨大なパラメータと作動モードが存在している。
そのために、従来のない組織横断のシステム開発タワーを設けることを推奨している。空調、電池、電費、NVHなどの部隊を跨る新しい体制で横連携を取る。システム間のトレードオフを究極に遂行し、最善なアーキテクチャを磨き上げ、最適なハードとソフトウェアの組み合わせを選定する。
日本のモノづくりの家の芸である”すり合わせ技”をさらに進化させる必要がある、ミリミリで公差を詰めて最良の品質と機能を実現するのは”システム開発が済んでいる”前提だった。下手するシステム開発で、いくらすり合わせしてもよいものが作れない。自分が思った最高のシステムと別人の思った最高のシステムを組み合わせた時に、最高のシステムになることは必ずしも保証がないことだ。
“CASE”の時代、不可欠になっているのはシステム全体を俯瞰して、無限大に近い設計空間から、市場に導入したい車に一番似合うシステムを鋭い目で探し出すことだと考えておる。これができれば、モノづくりの手戻りと目標性能の下方修正は開発後期で避けられる。中国市場で新車の開発スピードは異例的に速い、3年ペース新車開発ができている、どんどん新しい機能を載せた車をSOPして、きわめて早い戦いだった。歴史が浅い新興自動車メーカーなのに、なぜできているか、ほんとに品質を無茶にしているだけなのか。実は、今中国市場での新しい電気自動車、PHEVは非常に見栄えも、品質も良くできている。彼らが得意のは、優秀な若いエンジニアを集めて、豊富なローカルサプライチェーンから必要なものだけを見つかって、純粋に数値モデルをベースにした合理的なデザインと、徹底したシステム設計だった。
日本の自動車業界にMBD(モデルベースデザイン)を推進するのは、少なくとも下記3点が改善されると期待しておる。
- 自分都合
- 木を見て森を見ず
- 相手に不要な忖度